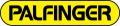
Палфингер Продукционстехник България ЕООД
About the company
Worldwide, PALFINGER stands for the most innovative, reliable and cost-effective lifting solutions for use on commercial vehicles and in the maritime field. With our technological expertise and experienced staff, we set quality benchmarks in the industries in which we operate. Sustainability and the responsible use of resources are at the core of all our actions. High flexibility and competence in production and a global sales and services network give us a crucial competitive edge and ensure our customers LIFETIME EXCELLENCE.
As a multinational company group with its headquarters in Salzburg, Austria, PALFINGER has manufacturing and assembly sites in Europe, North and South America and Asia as well as over 4,500 sales and service centеrs located in over 130 countries across five continents.
The core product is the Loader Crane. The company is the world market leader in this segment with close to 150 models and a market share of more than 30 percent. In Timber and Recycling Cranes on- and off-road as well as Container Handling Systems PALFINGER is also the world’s biggest manufacturer. Over the years the product portfolio has been steadily expanded with products such as the Truck Mounted Forklifts, Tail Lifts, and the Access Platforms. With our Railway Systems and Bridge Inspection Units we are European technology and market leader in this high-tech sector. Farm Cranes as well as Truck Bodies and Pick-up Tail Lifts complete the product range. PALFINGER MARINE is one of the leading manufacturers of innovative and customized Marine, Offshore and Wind Cranes as well as Launch & Recovery Systems. Today, PALFINGER is a worldwide group that is always close to the customer, no matter the location. In 2013, the PALFINGER Group has been awarded the most significant contracts for its marine business in the total equivalent amount of approx. EUR 90 million. To complete its product portfolio in the marine business, PALFINGER took over Norwegian Deck Machinery AS, a manufacturer of special winches for the marine and offshore industry. This participation gives PALFINGER access to customer groups that have so far not been addressed.
Palfinger Produktionstechnik Bulgaria EOOD has been established 15 years ago and has 2 factories – one in Tenevo, which manufactures hydraulic cylinders and another one in Cherven Bryag, where metal components for cranes are produced to be exported to Slovenia and Austria. The large investment in Bulgaria aims to achieve a closed (full-cycle) manufacturing process by 2019. Until now, the overall investment in Bulgaria amounts nearly €50 million.
Currently, in Bulgaria, we employ 1024 people, of whom 500 are located in Cherven Bryag and our development strategy is to increase their number to 800 in the next 5 years. The new expansion of our local production will proceed in three stages. An area of about 60 acres purchased by the enterprise over the past two years will be used to build three plants - welding, painting and assembly. €15 million is provided entirely from the parent company Palfinger AG with the aim to develop a high-tech assembly unit in Bulgaria. The first expansion phase has a budget of €5.35 million and will be invested to build a welding compartment, infrastructure and covered storage areas. Construction has already begun and is expected to be completed in October 2016.
As one of the largest employers of specialists from various occupations within the vocational field of „Mechanical Engineering, Metalworking and Metallurgy“, we have strong interest in supporting the development of innovative and high-quality education and training to ensure our future employees possess the right knowledge, skills and competencies to apply in their everyday job, but also to ensure transferability of their learning outcomes, which would not only increase their employability, but would also ensure that our bespoke European quality standards are met.
We apply the following quality management systems: ISO/TS16949 (aimed at the development of a quality management system that provides for continual improvement, emphasizing defect prevention and the reduction of variation and waste in the supply chain) and PPAP (Production Part Approval Process).